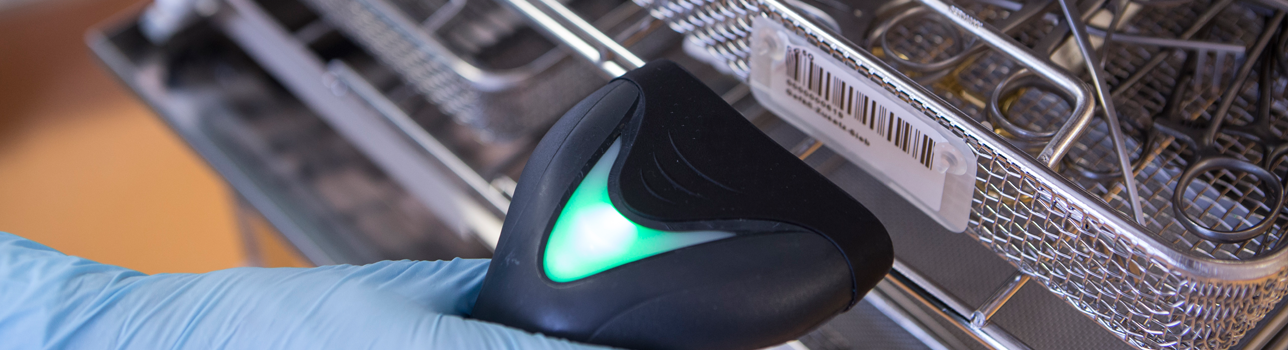
Supplier Management
Quality, supply reliability and efficiency: these three aspects are at the forefront of supplier management at RHÖN-KLINIKUM AG. Material for medical equipment and medical supplies is procured almost exclusively through external suppliers. For regular hospital processes, that involves certain risks, for example as a result of supply shortages or quality issues. By ongoing market and product monitoring we ensure that dependencies on sole suppliers, single products and service providers are kept to a bare minimum. In principle, we moreover work together with at least two suppliers for each product group to keep the probability of failure as low as possible.
With only a few exceptions, supplier management is centralised. As a rule, products and services needed at only one site are handled by the respective facility itself. Group product and supplier responsibility for certain product groups such as knee and hip prostheses, heart valves, defibrillators or cardiac pacemakers as a general rule is assumed by two materials management heads from different hospitals.
Ensuring availability of medical devices and pharmaceuticals is an ongoing challenge for the medical facilities of RHÖN-KLINIKUM AG. After company mergers or takeovers, certain products are frequently no longer distributed for reasons relating to margins or competition. In these cases it is important to act quickly to ensure that our treatment quality can still be maintained. The situation is similar when follow-on products come at a higher price. In the interest of efficiency, we rely in these instances on alternatives and competitors.
All products are transported for RHÖN-KLINIKUM AG by lorry, rail, air and ship. Since deliveries of supplies are performed by forwarding agents, we do not have any influence on their transport emissions. When selecting such service providers, however, we make sure that they maintain certified environmental management systems. Given the disproportionately high cost, we do not record other transport emissions such as those from business trips or the commute by employees. Compared with the previous year, materials and consumables used declined by 103.3 million euros or 24.3 per cent to 321.8 million euros (previous year: 425.1 million euros), essentially due to the sale of subsidiaries concluded in the previous year. The materials ratio rose from 28.1 per cent to 29.0 per cent as a result of use of articles entailing higher material costs at our facilities.